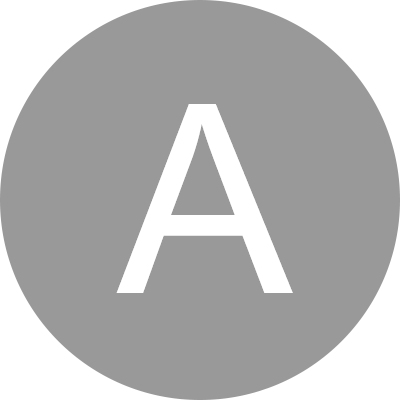
In the automotive cooling system hoses, using para-aramid as the reinforcement skeleton material can operate normally for a long time under working conditions from -196℃ to 204℃, significantly enhancing the performance and stability of the cooling system hoses.
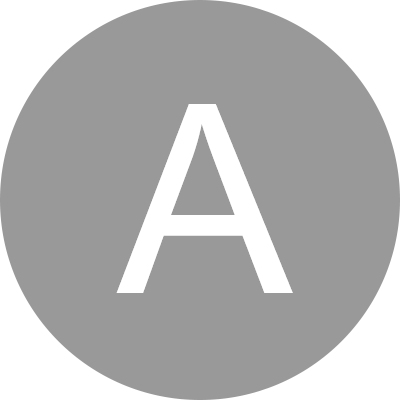
To address issues such as hose bursting and cracking, solutions can be implemented by enhancing material strength, improving metal component design, and adjusting hose formulations. For example, measures such as increasing the diameter of the wire rope and optimizing the design of metal components can effectively improve the pressure resistance and burst pressure of the hose, reducing the risk of bursting and cracking.
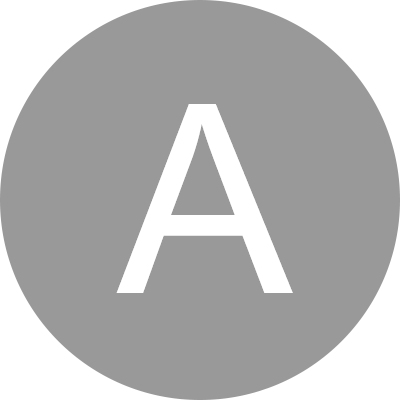
Composite hoses are a type of pipeline product made up of multiple layers of materials, primarily consisting of an inner steel wire, a reinforced woven layer, a sealing layer, an outer reinforcement layer, and an outer steel wire. This multi-layer structure allows composite hoses to perform excellently in terms of resistance to pressure, chemicals, and temperature. Composite hoses play a key role in areas such as oilfield cementing, workover, and petroleum geological exploration, capable of transporting fluids such as mud and water at normal temperatures, and they exhibit good chemical resistance, allowing them to operate stably in various harsh environments. Additionally, composite hoses are widely used in oil, chemical transport vessels, docks, and other locations, and their resistance to bending ensures that they do not crack or delaminate even under frequent bending.
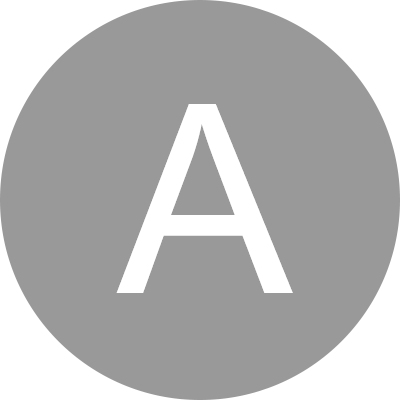
Rubber joints, as a key pipeline accessory, play an important role in oil transportation pipelines. With their good elasticity and flexibility, they can significantly absorb vibrations, compensate for pipeline displacements, and reduce noise, thereby improving the reliability and durability of the entire oil transportation system. As a professional enterprise in the high-end rubber joint manufacturing field, the company's rubber joints possess characteristics such as efficient shock absorption, high-temperature resistance, and corrosion resistance, making them suitable for various complex working conditions. For example, their rubber joints can maintain good shock absorption effects even when facing high-frequency vibrations, and they can still exhibit stable performance under high temperatures and corrosive media.
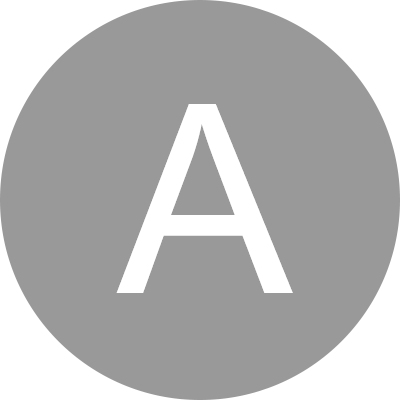
In the petrochemical industry, the quality control of hose installation and construction is crucial. Before construction, it is necessary to strictly follow the drawings to ensure the use of appropriate materials and fittings. During the construction process, detailed construction records should be prepared, and strict quality inspections should be conducted on each section of the pipeline. In pipeline welding construction, operations should be carried out strictly according to welding standards, and non-destructive testing should be performed on the weld surfaces to ensure the welding quality is qualified. In addition, the anti-corrosion treatment of the pipeline is also very important, requiring the selection of appropriate anti-corrosion materials and application according to specifications to enhance the service life and stability of the pipeline.
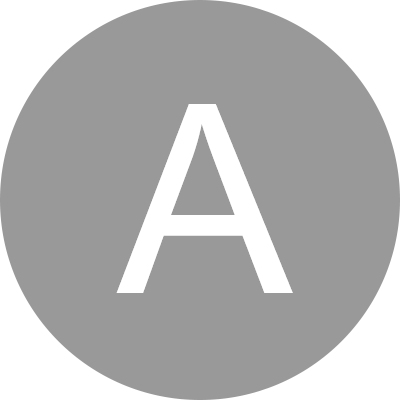
The mining gas rubber hose solution is suitable for gas extraction in coal mines and the transportation of other mining media. This hose has good bending performance, anti-static properties, flame resistance, wear resistance, and corrosion resistance, making it particularly suitable for use in coal mine gas extraction systems, drilling hole sealing, and other related fields. Its customized service can adjust the hose size and performance parameters according to customer needs, ensuring a perfect match for specific usage scenarios, improving work efficiency, and reducing operating costs.